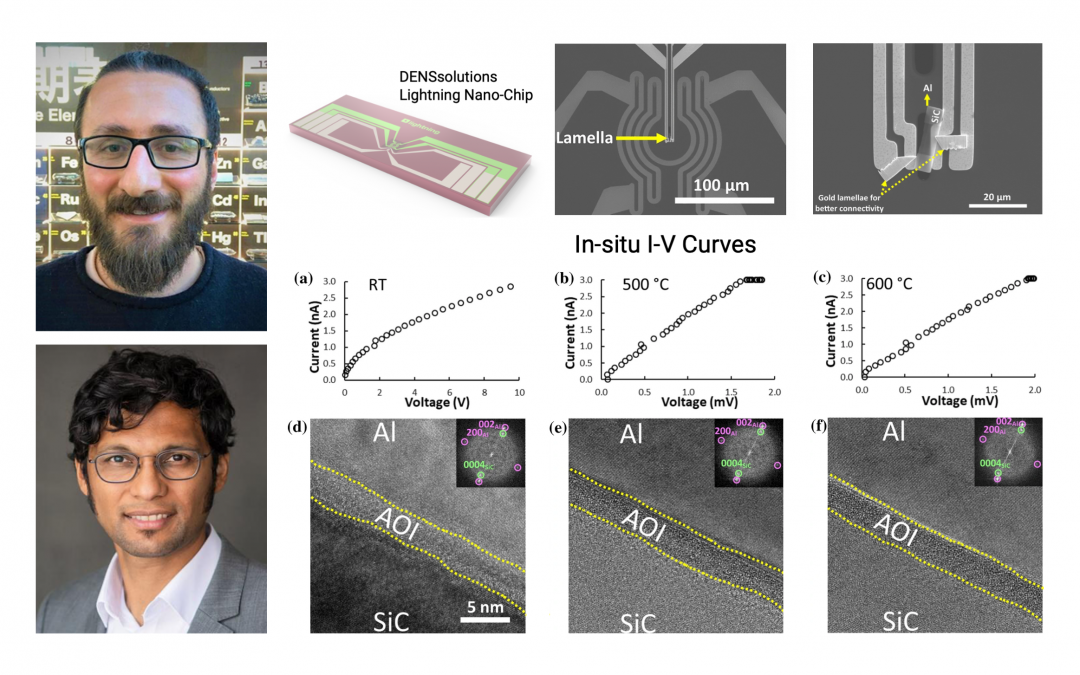
DENSsolutions’ Lightning system helps uncover the interaction mechanism in reactive metal-ceramic system, Al-SiC
Using the DENSsolutions Lightning system, researchers were able to provide an electrical, chemical and structural analysis of the Al–amorphous SiO₂–SiC interface at high temperatures.
Original article by Adabifiroozjaei et al.
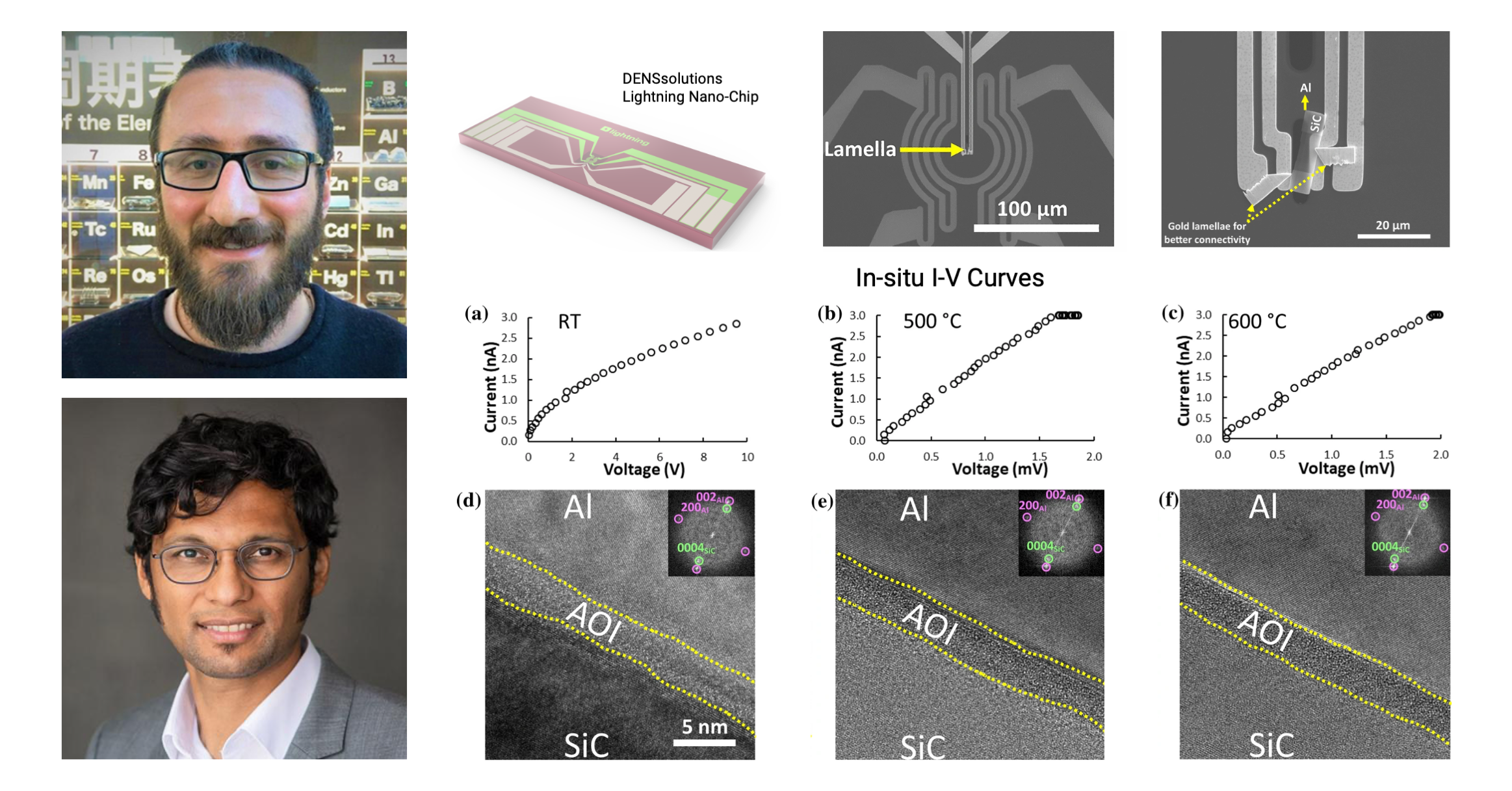
The use of hybrid materials containing both metals and ceramics has become increasingly popular within manufacturing and microelectronic industries due to their optimized and well-balanced properties. Aluminum-silicon carbide (Al-SiC) is a widely known metal-ceramic composite material, commonly used in microelectronic packaging for automotive and aerospace applications. In Al-SiC an amorphous oxide layer (AOL) of SiO₂ is known to exist between the Al and SiC. Notably, the mechanism of interaction between the reactive metal (Al) and ceramic (SiC) and the AOL (SiO₂) under the heat-treatment process is still not well-understood. In fact, numerous theories about the interaction mechanism have been proposed over the past few decades. The major problem is that the studies conducted so far, regardless of the mechanism proposed in them, were ex situ and therefore not capable of resolving the atomic-scale nanostructural and chemical changes occurring at the interfaces during the heat-treatment process. In a recent paper published in the Journal of Materials Science, involving our valued users at TU Darmstadt, Dr. Esmaeil Adabifiroozjaei and Dr. Leopoldo Molina-Luna, the DENSsolutions Lightning system was utilized to reveal the evolution mechanism of the Al–AOL–SiC system under heating and biasing conditions. This study involved a team of researchers from institutes all over the world, including the University of Tabriz in Iran, NIMS and Shibaura Institute of Technology in Japan, and UNSW Sydney in Australia.
Sample preparation
The first step for Dr. Adabifiroozjaei and his fellow collaborators was to carefully prepare the Al-SiC sample. After ultrasonically cleaning the SiC wafer, removing the oxide layer and allowing its regrowth by inserting the wafer into a desiccator, an Al layer with a thickness of ~1 µm was sputtered on the wafer using Shibaura’s CFS-4EP-LL sputtering machine. Next, in order to prepare the lamella, the researchers applied focused ion beam milling using JEOL’s JIB-4000 FIB. The prepared lamella was then loaded onto the DENSsolutions Lightning Nano-Chip (see Figure 1a). The low- and high-magnification scanning electron microscopy (SEM) images of the chip and the loaded lamella are shown below in Figure 1b) and 1c), respectively. Next, an Au lamella was prepared by FIB and connected to Al–AOL–SiC lamella and chip in order to ensure electrical current passes through Al–AOL–SiC lamella.
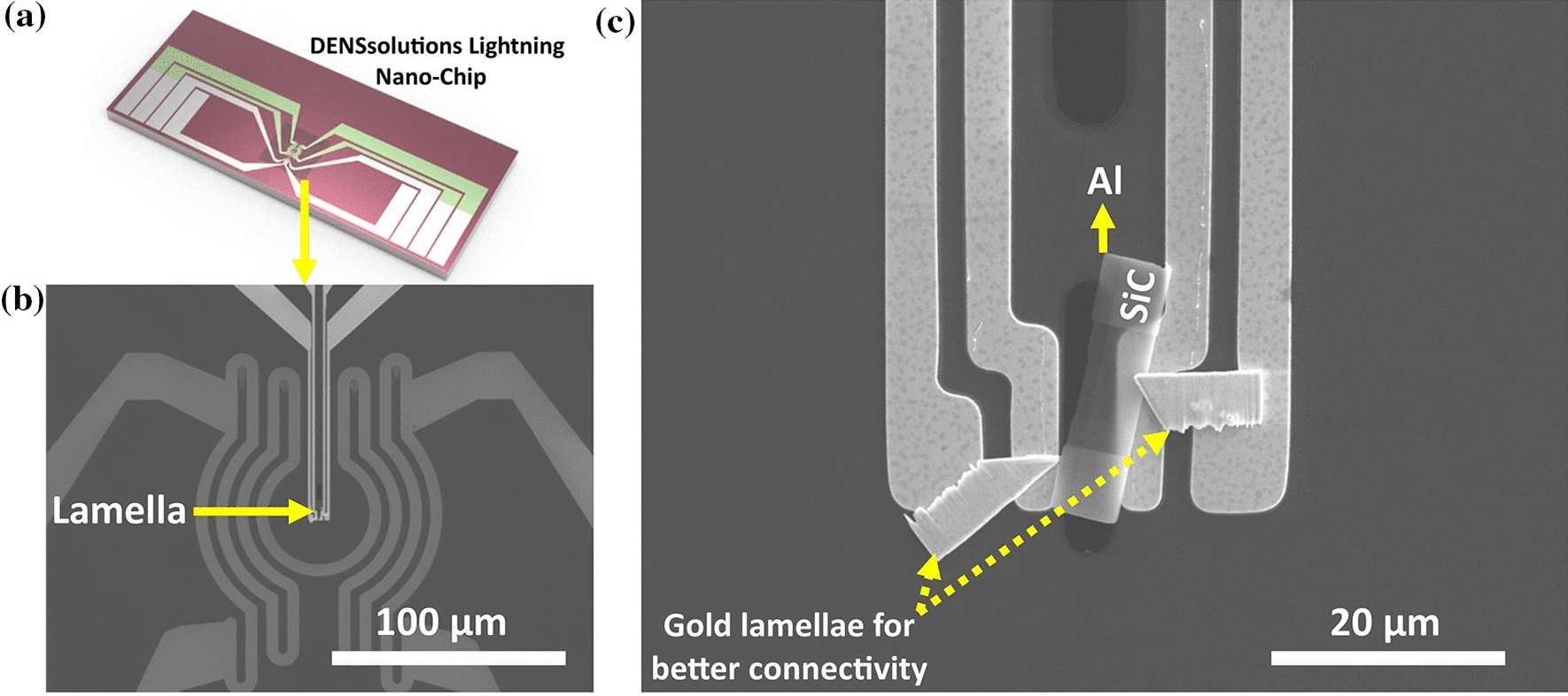
Figure 1: a) DENSsolutions Lightning Nano-Chip used for the in situ heating and biasing experiment, b) low- c) and high-magnification SEM images of the loaded lamella on the Nano-Chip, respectively.
Experimental results
The researchers performed EDX and EELS elemental mapping to determine the chemical composition of the phases across the Al–AOL–SiC interface. The EDS mapping of the interface is shown in Figure 2a), while the high-resolution EELS elemental mapping of the interface is shown in Figure 3b) – both of which reveal the consistent presence of a narrow oxide layer with a thickness in the range of 3–5 nm.
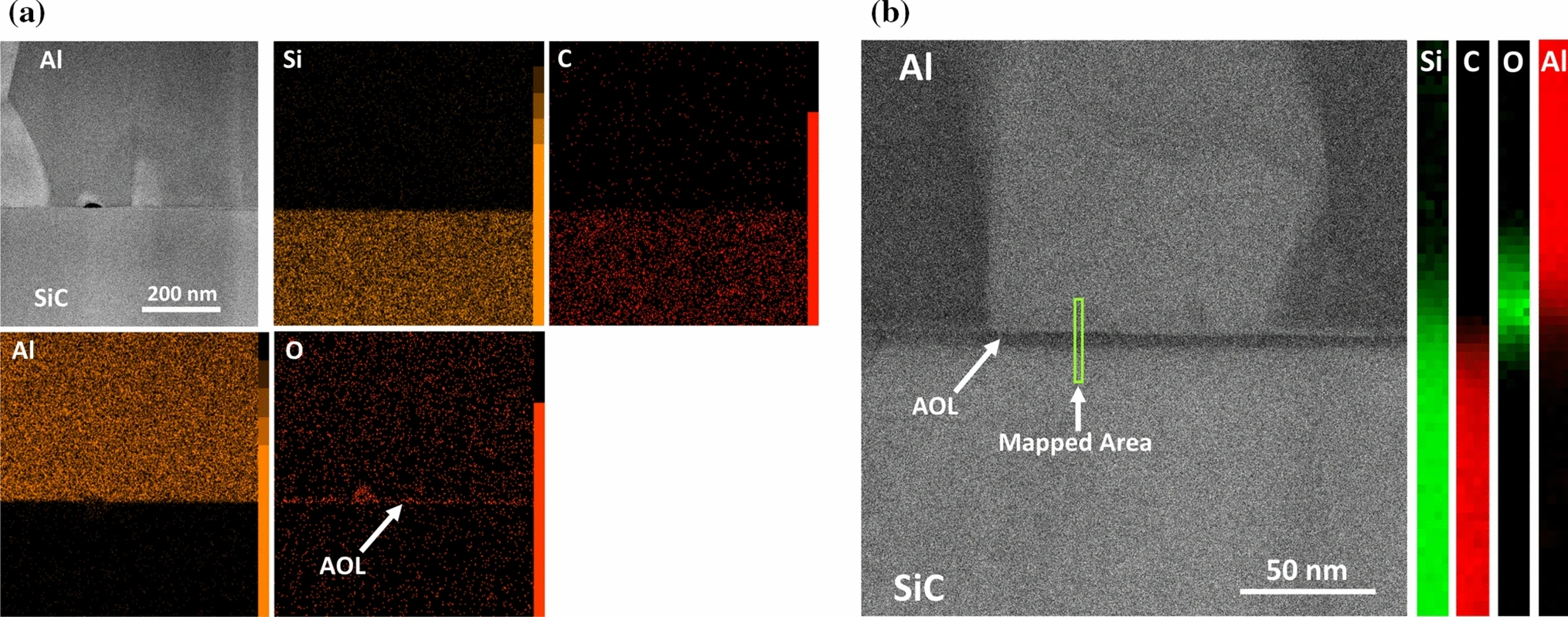
Figure 2: a) EDS elemental mapping of Al–AOL–SiC interface, showing the presence of the AOL, b) STEM-HAADF image of Al–AOL–SiC interface and its EELS map profile.
Next, the researchers began with the in situ heating and biasing experiment to study the electrical characteristics of the lamella. First, a compliance current was set to 3 nA, then the voltage required to reach such a current was recorded at each temperature. The acquired I–V curves for room temperature, 500 ° and 600 °C after 30 minutes of application of the field are presented in Figure 3a–c), respectively. The I–V curves and high resolution TEM images (shown in Figure 3d–f) indicate that the resistivity of the Al–AOL–SiC device decreased three orders of magnitudes at 500 °C with no apparent change in the nanostructure.
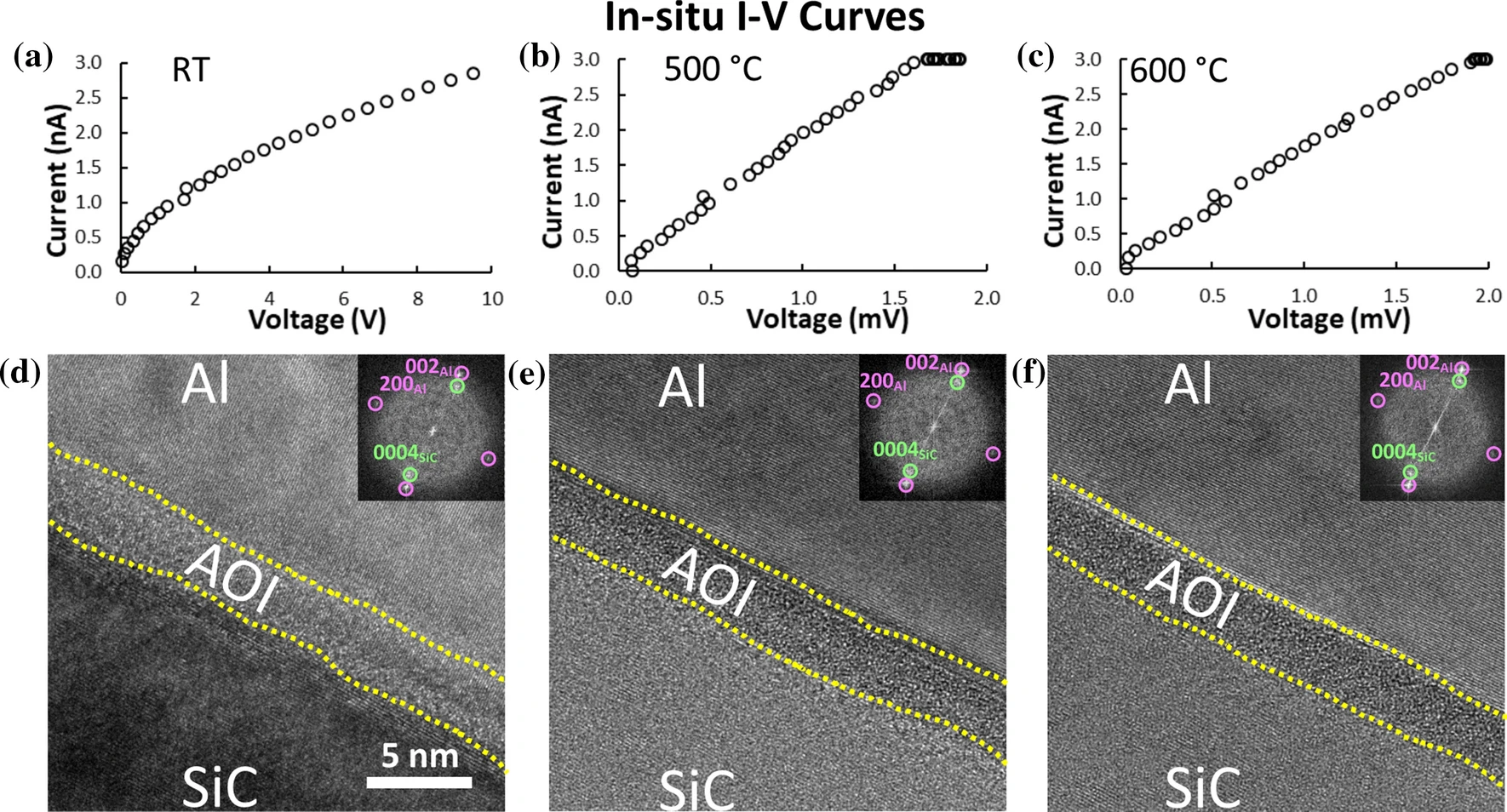
Figure 3: a), b), and c) show the I–V curves of Al–AOL–SiC interface measured at room temperature, 500° and 600 °C, respectively. d), e), and f) show the high-magnification images of Al–AOL–SiC interface from a small area of low-magnification images.
The chemical changes occurring at the interface during the heating process were investigated on another lamella using the same DENSsolutions Lightning holder, but on a Wildfire (heating-only) Nano-Chip. HAADF-STEM images and EELS chemical profiles were acquired and the results are shown in Figure 4 below.
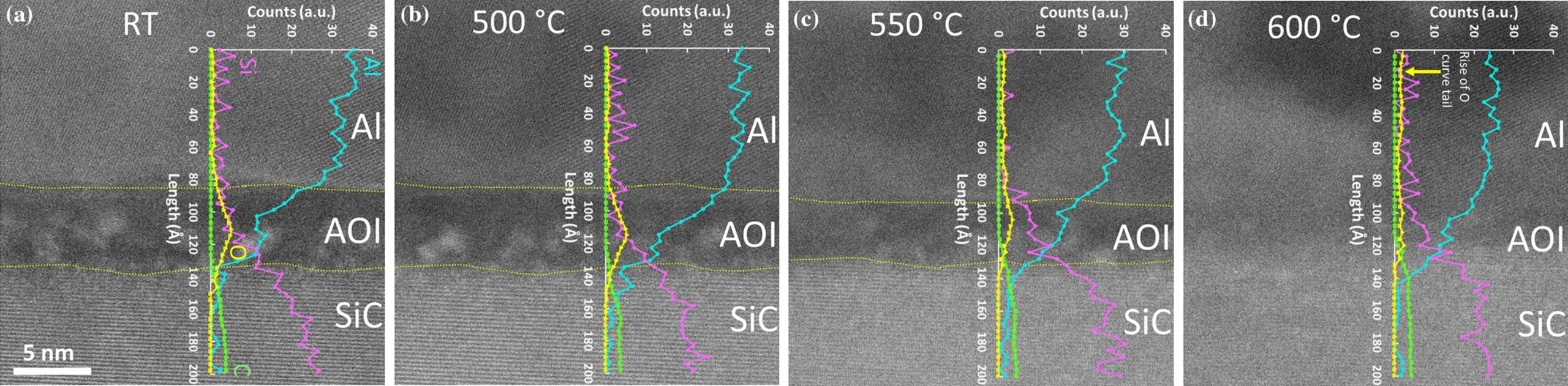
Figure 4: a), b), c ) and d) show changes in chemistry (line profiles of Al (Aqua), Si (Violet), C (Lime), and O (Yellow)) of Al–AOL–SiC interface at room temperature (25°), 550°, 500° and 600 °C, respectively.
During this analysis, the researchers observed that at 550 °C, the AOL width was reduced, which was specifically due to AOL dissolution into the Al. Moreover, the analysis of the structural changes at the interface nanostructure at 600 °C showed that the dissolution of the SiO₂ amorphous layer resulted in the formation of α-Al₂O₃ and Si within the Al. In contrast, the elemental interdiffusion (Al³⁺ ⇄ Si⁴⁺) between Al and SiC was observed to occur, resulting in formation of Al₄C₃. From the results, we can infer that the reaction mechanism between Al and crystalline SiC is different with that between Al and SiO₂ amorphous phase.
Conclusion
Dr. Adabifiroozjaei and his fellow collaborators performed a comprehensive in situ STEM heating and biasing study using the DENSsolutions Lightning system, investigating the electrical, chemical and microstructural features of the interface of a Al–AOL–SiC system. Performing this study under an ultrahigh resolution of 4 Å allowed the researchers to confirm, for the first time in literature, that the reaction mechanism between reactive Al and crystalline SiC is different than between Al and amorphous SiO₂. Specifically, they found that whereas the reaction between SiO₂ and Al follows the dissolution mechanism, the reaction between SiC and Al proceeds through elemental interdiffusion. Importantly, these findings might be applicable to other reactive metal-ceramic systems that are currently used in manufacturing and electronic industries.
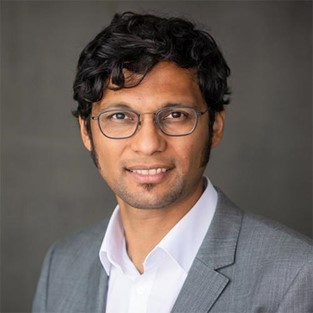
“With the stability and accuracy provided by DENSsolutions Lightning system, we could reveal features of an interfacial interaction in a common metal-ceramic system (Al-SiC) that were not previously observed. Such studies at very high resolution are absolutely necessary for the understanding and future development of composite materials at elevated temperatures.”
Prof. Dr. Leopoldo Molina-Luna Professor | TU Darmstadt
Original article:
Discover our Lightning solution:
Discover more publications made possible by Lightning:
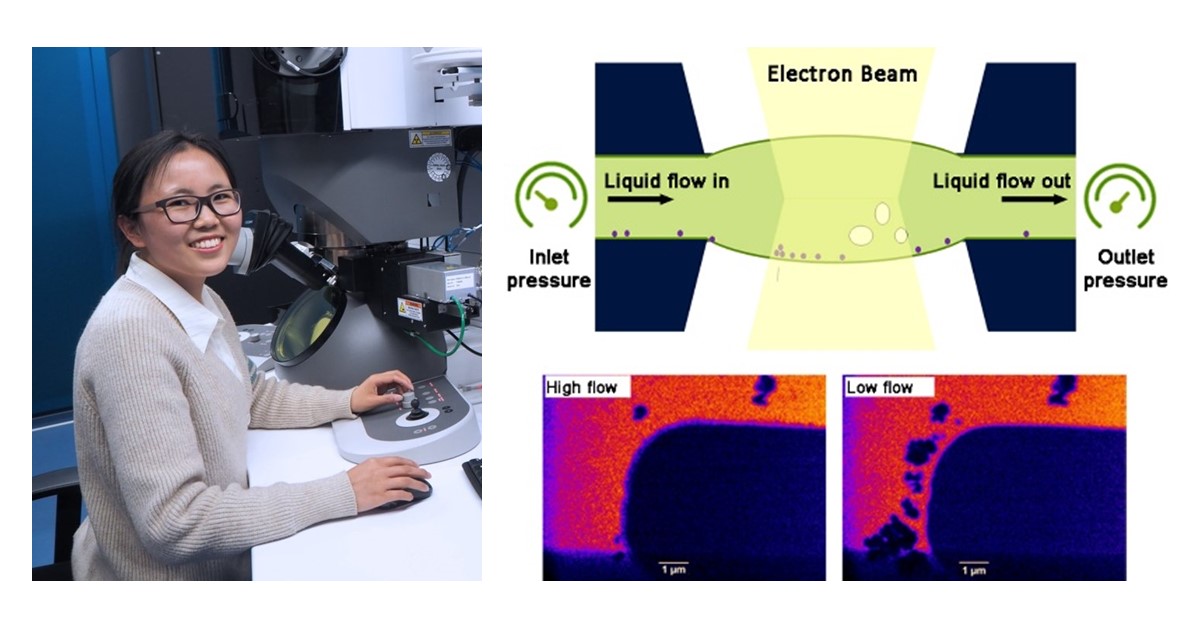
Liquid flow control: Unlock untapped research capabilities within in situ LPEM
Using the DENSsolutions Stream system, researchers were able to create a highly controlled chemical environment for visualizing the nanoscale metallic electrodeposition of copper crystals.
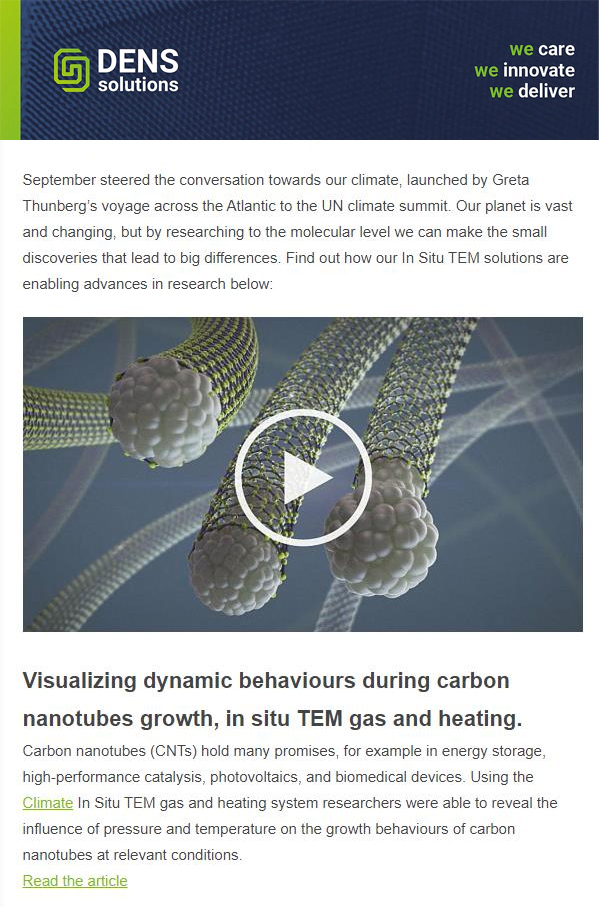